Supply Chain
Click to review the various offerings of the Supply Chain Impact Program:
Supply Chain Skills for Excellence Series | Indiana SRM Platform | Articles & Publications
Supply Chain Impact Program
Indiana manufacturers continue to navigate a volatile supply chain environment marked by persistent cost pressures, dynamic geopolitical landscapes, and unpredictable supply disruptions. The key supply chain challenges include:
- Rising costs and inflationary pressures in raw materials, labor, and logistics
- Supply disruptions caused by raw material shortages, supplier capacity constraints, and geopolitical tensions
- Optimizing inventory levels, minimizing stock-outs, yet improving cash flow
- Managing supply risks and supplier performance
- Investing and adopting new technology to improve supply chain visibility and decision-making
To help and support Indiana manufacturers successfully manage these challenges, Purdue MEP has created a Supply Chain Impact Program. This program is designed to help small manufacturers tackle these challenges by equipping them with the skills, tools, and strategies needed to optimize supplier relationships, manage costs, improve inventory control, and enhance supply chain resilience.
The Supply Chain Impact Program includes:
- Strategic Sourcing Skills for Excellence workshops
- Material Planning and Inventory Management Skills for Excellence workshops
- Supply Chain consulting services such as supplier search capability
- Assessment of a company’s Supply Chain capability and improvement areas
- Access to the Indiana SRM (Supply Relationship Management) Platform
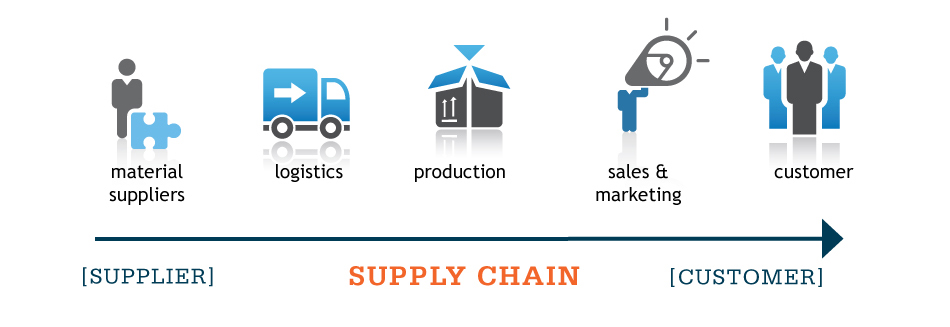
Supply Chain Skills for Excellence Series:
Drive supply value, build supplier relationships, improve inventory and material planning efficiencies, and enhance your negotiating and financial skills with Purdue MEP’s Supply Chain workshops. These workshops are designed as individual workshops or as two Skills for Excellence series for professional development.
These workshops combine real-world case studies with interactive exercises and provide practical templates to help you elevate your supply chain capabilities. Participants will leave with actionable insights to improve their supply chain’s value, boost competitive advantage, and drive financial performance while improving customer satisfaction.
Strategic Sourcing Skills for Excellence: Optimizing Supplier Performance
This comprehensive training series is designed to equip supply chain professionals with the essential skills needed to drive cost efficiency, supplier collaboration, risk management, and contract effectiveness.
Covering supply chain finance, strategic supply management, contract negotiations, and risk resilience, participants will gain hands-on experience in financial analysis, negotiation strategies, and risk mitigation tools. Through interactive exercises, real-world case studies, and actionable frameworks, this series empowers attendees to enhance sourcing strategies, improve supplier relationships, and build resilient, high-performing supply chains.
Workshop Content and Series Schedule:
The Strategic Sourcing Skills for Excellence series consists of four one-day workshops (click each title for additional information):
- Supply Chain Financial Essentials: Optimizing Cash Flow and Profitability
- Contracting and Negotiations for Supply Chain Management
- Mastering Strategic Supplier Management
- Supply Chain Risk, Resiliency, and Relationship Management
Who Should Attend:
The Strategic Sourcing Skills for Excellence series is designed for professionals in procurement, supply chain management, and operations who want to enhance their strategic sourcing capabilities and supplier management skills.
- Purchasing Managers & Buyers – Enhance negotiation skills, supplier evaluation techniques, and contract management expertise.
- Supply Chain & Procurement Professionals – Improve financial decision-making, category management, and supplier risk strategies. Enhance supplier relationships
- Operations & Materials Managers – Learn to align sourcing strategies and inventory planning with production needs and overall business goals.
- Supply Chain Leaders and Small & Medium-Sized Business Owners – Develop a resilient supply chain strategy and build supplier relationships to drive achievement of business goals via greater supply chain performance
Material Planning and Inventory Management Skills for Excellence Series: Driving Operational Value
This comprehensive training series equips supply chain professionals with the essential skills to optimize inventory, effectively manage material marketplaces, improve forecasting, and align financial strategies with operational goals.
Covering supply chain fundamentals, inventory management, material control and replenishment, S&OP (sales and operations) planning and financial skills, participants will gain hands-on experience in inventory classification, warehousing techniques, replenishment strategies, demand forecasting, and cost control. Through interactive exercises, real-world case studies, and actionable framework, this series provides the tools needed to enhance supply chain agility, improve cash flow, and drive operational efficiency in today’s dynamic business environment.
Workshop Content and Series Schedule
The Material Planning and Inventory Management Skills for Excellence series consists of four one-day workshops (click each title for additional information):
- The Essentials of Supply Chain Management
- Inventory Management Playbook: Tools and Strategies for Success
- S&OP Planning: Forecasting, Capacity, and Performance Excellence
- Supply Chain Financial Essentials: Optimizing Cash Flow and Profitability
Who Should Attend:
- Materials Managers & Planners: Enhance your skills in demand forecasting, materials requirement planning, and inventory optimization.
- Inventory Analysts & Controllers: Learn advanced techniques for inventory tracking, control systems, and cost optimization strategies.
- Supply Chain & Operations Leaders and Professionals: Align supply chain processes with organizational goals through effective supply planning and management.
- Production & Manufacturing Managers: Integrate production schedules with materials planning to ensure seamless operations.
Indiana SRM Platform
Indiana manufacturers continue to navigate a volatile supply chain environment marked by persistent cost pressures, dynamic geopolitical landscapes, and unpredictable supply disruptions.
To support and assist Indiana manufacturers overcoming these challenges, Purdue MEP is introducing the Indiana SRM (Supply Relationship Platform.
Powered by Sustainment, this low-cost solution helps manufacturers manage their supply chain, communicate with, collaborate with, manage performance, and identify new suppliers. The link below connects you with the Indiana SRM Registration Site and Sustainment-powered platform.
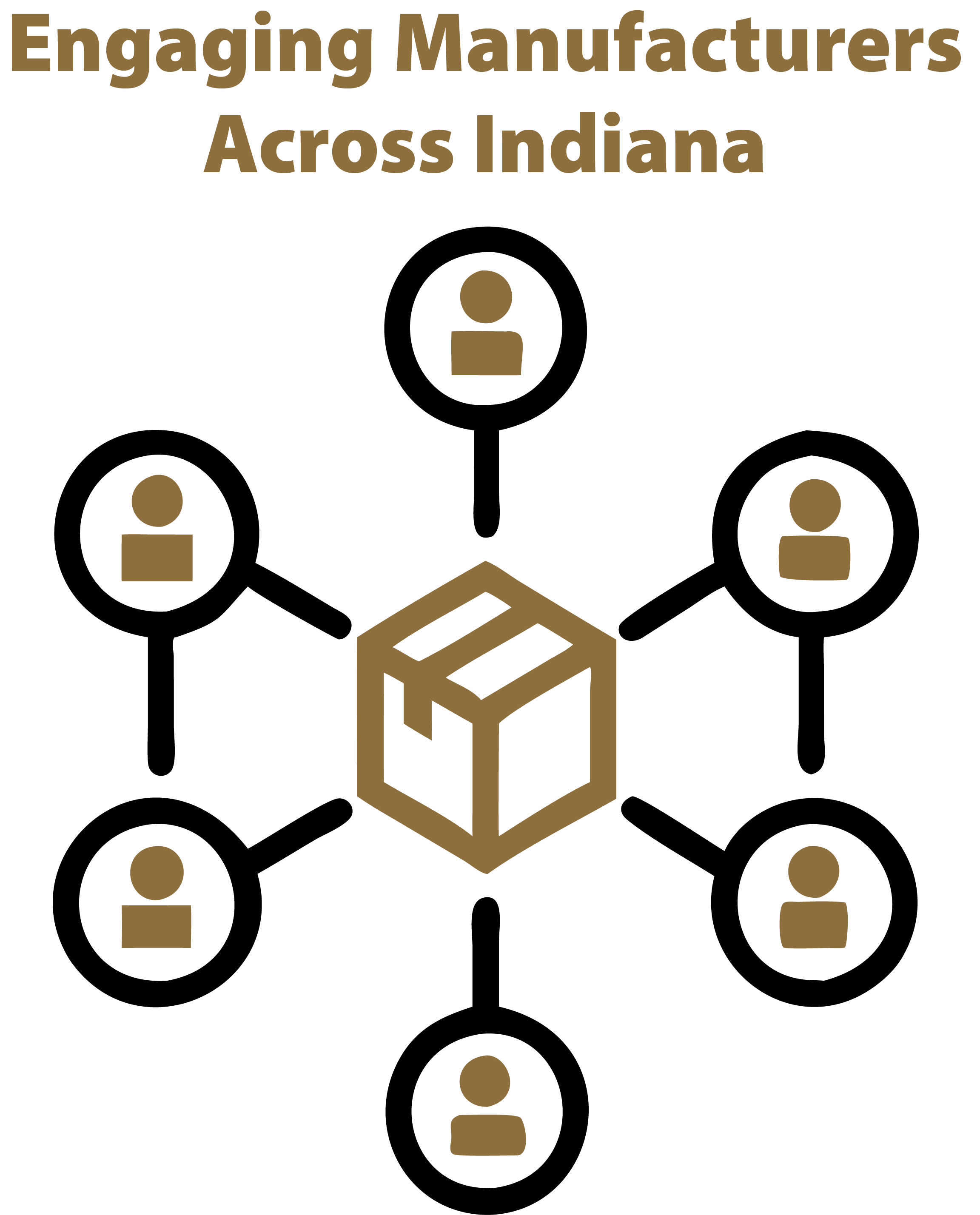
Articles & Publications
- Building Lasting Resilience in Your Supply Chain
- Driving Cost Value in Your Supply Chain
- How U.S. Manufacturers Can Take Advantage of Reshoring (white paper)
- How Manufacturers Can Take Advantage of Reshoring and Regionalization Trends - Thomas.net
- There's More to Cost than Cutting - Inside Supply Management magazine
- Additive Manufacturing
- Collaborative Robotics Assistance
- Cybersecurity
- Digital Manufacturing & Design Assessments
- Digital Manufacturing Technology Center (DMTC)
- Digital Transformation and AI Technologies
- Employee Attraction & Retention
- Executive Peer Groups
- ExporTech™
- Food and Beverage
- Leadership Development
- Lean Manufacturing
- Lean Office
- Onboarding
- Quality
- Six Sigma
- Supplier Scouting Network
- Supply Chain
- TAP InDev
- Training Within Industry
Contact

Supply Chain Services Specialist